NFPA 101 and Carbon Monoxide Detection: A Brief Overview
The NFPA 101 Life Safety Code requires CO detection in many types of occupancies, particularly where fuel-burning appliances, fireplaces, or attached garages exist. As CO is a colorless and odorless gas, its detection is essential to prevent poisoning, which can lead to serious health issues or even fatalities.
While both new and existing buildings must meet CO detection standards, the extent and type of detection system required differ based on whether the building is newly constructed or an existing structure. These differences are designed to balance safety with the practical challenges of retrofitting older buildings.
Key Differences Between New and Existing Buildings
1. Location of CO Detectors
-
New Buildings: In new constructions, CO detectors are generally required in all areas with fuel-burning appliances or attached garages. This includes sleeping areas and common areas that may be adjacent to these high-risk spaces.
Action for Maintenance Managers:
- Ensure that CO detectors are installed throughout the building in all relevant areas. Pay special attention to sleeping areas and spaces near fuel-burning appliances or garages.
- Verify that the detectors are interconnected so that when one alarm sounds, all others in the building do as well. This ensures that occupants in distant areas are alerted in case of a CO leak.
- Include CO detectors in your routine inspection schedule to confirm they are functional and have battery backups in place.
-
Existing Buildings: In older buildings, CO detectors may not need to be installed building-wide. Instead, the focus is on high-risk areas, such as spaces directly adjacent to fuel-burning appliances or garages.
Action for Maintenance Managers:
- Identify high-risk areas and ensure that these spaces are equipped with CO detectors. Start with sleeping areas or areas immediately adjacent to fuel-burning sources.
- Battery-operated detectors may be more practical in older buildings where hard-wiring systems may be challenging. Make sure these detectors are properly maintained and checked regularly.
- If upgrading to a newer detection system is feasible, consider adding interconnected CO alarms for broader coverage without extensive retrofitting.
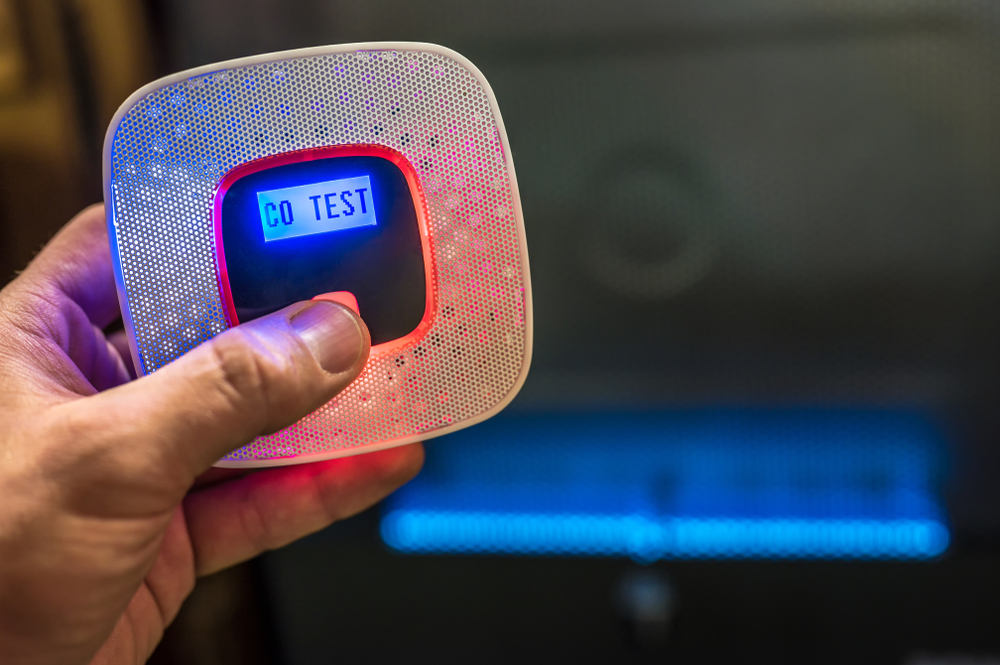
2. System Design and Installation
-
New Buildings: CO detectors in new constructions are required to be hard-wired into the building’s electrical system, with battery backups to ensure continuous operation during power outages.
Action for Maintenance Managers:
- During regular inspections, check that all CO detectors are securely connected to the building’s electrical system and that backup batteries are functional.
- If expansion or renovations occur, ensure that any new areas are integrated into the existing detection system.
-
Existing Buildings: In existing buildings, battery-operated CO detectors are often permitted, especially if installing hard-wired systems would require major renovations.
Action for Maintenance Managers:
- Develop a routine battery replacement schedule to ensure that CO detectors remain operational. Keep spare batteries in stock, and use scheduled reminders to ensure batteries are changed regularly.
- If the building already has a fire alarm system in place, consider integrating CO detection with this system to simplify maintenance and notification processes, if possible.
3. Audible and Visual Alarms
-
New Buildings: CO detectors in new buildings must provide both audible and visual alarms, particularly in sleeping areas and for buildings that house individuals with hearing impairments.
Action for Maintenance Managers:
- Test the audibility and visibility of alarms in all relevant spaces during routine safety checks. Ensure that visual alarms meet the needs of any hearing-impaired occupants.
- Conduct fire and CO drills that include testing the response to these alarms, ensuring that occupants recognize the distinct sound of a CO alarm compared to other alarm systems.
-
Existing Buildings: Existing buildings may not require visual notification systems, but audible alarms should still be present, especially in areas where occupants sleep or may be unaware of a CO leak.
Action for Maintenance Managers:
- Focus on testing the audible alarms regularly to ensure they are loud enough to wake occupants, especially in sleeping areas.
- If your building houses occupants with hearing impairments, consider adding visual alarm devices during future upgrades, even if they are not strictly required.
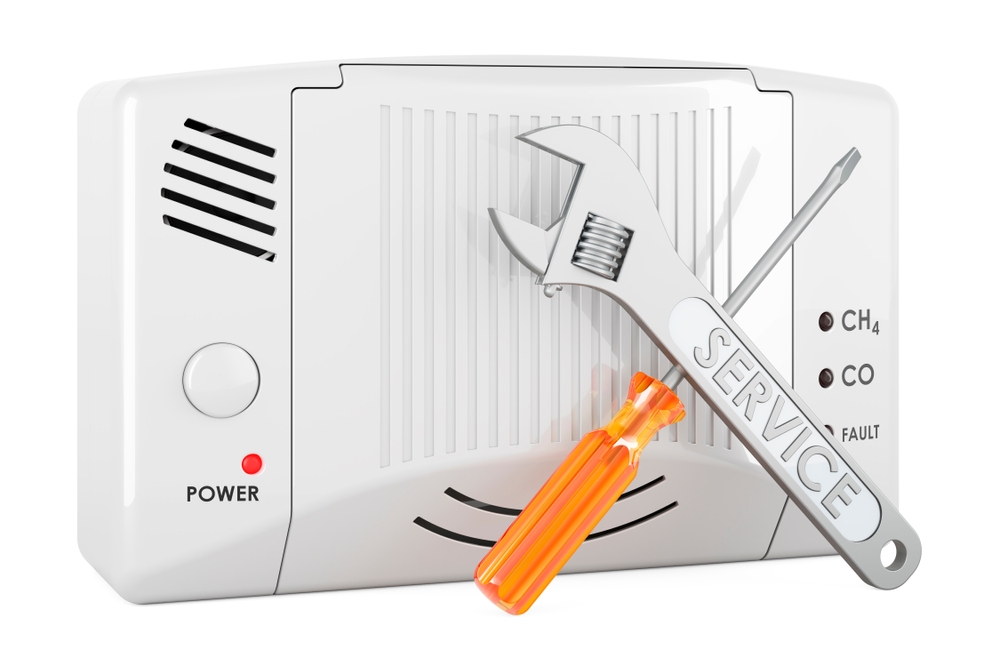
Maintenance Recommendations
To keep both new and existing buildings in compliance with NFPA 101 and ensure the safety of all occupants, consider these maintenance best practices:
For New Buildings:
- Conduct regular inspections of all CO detectors and ensure they are interconnected across the entire facility.
- Include CO alarms in your building-wide alarm tests to verify proper function and to educate occupants on the alarm system’s sound.
- Keep detailed logs of maintenance checks, battery replacements, and system tests to ensure compliance with both the NFPA 101 and local regulations.
For Existing Buildings:
- Identify critical areas for CO detection, focusing on high-risk areas like sleeping quarters and spaces near fuel-burning appliances.
- Establish a routine battery replacement schedule and ensure alarms are always functional.
- Consider future upgrades that could interconnect CO alarms with the fire alarm system, improving the overall safety of the building.
Final Thoughts
Whether managing a new or existing building, maintenance managers play a key role in ensuring the proper functioning of carbon monoxide detection systems. By following the NFPA 101 standards and adopting a proactive approach to maintenance and testing, you can significantly reduce the risk of CO poisoning and ensure the safety of all building occupants.