Hazardous Locations Electrical Systems: How to Educate Your Employees
Industrial facilities often contain hazardous locations. These areas have the potential to cause or contribute to serious harm to surrounding structures and nearby employees. Employers and their workers both gain great benefit from formal training that teaches technicians how to safely work in and navigate hazardous locations.
What is a Hazardous Location?
According to OSHA (the Occupational Safety and Health Administration), these types of locations qualify as hazardous. Employers and employees need to take special precautions when working in these environments to minimize the risk of death, injury, and damage.
- Class I locations contain flammable gases that increase the risk of arc flashes, explosions, and fire. Gases in a liquid state are included in this classification.
- Class II locations are characterized by flammable dust and particles. When airborne, these particles increase the risk of explosions.
- Class III locations contain flammable fibers and other materials. While these materials are needed during regular industrial operations, they increase the probability of dangerous fires and out-of-control combustion.
These classes are further divided into divisions and zones. These clarifications refer to the subtle differences in hazardous conditions that call for a variety of PPE (personal protective equipment) and safety procedures.
In an industrial setting, hazardous locations can be:
- Storage spaces
- Production environments
- Electrical control rooms
- Generator rooms
A familiarity with the standards surrounding hazardous location safety is essential for all who participate in industrial activities.
Employee Safety Tips for Hazardous Locations
There are some important steps that workers should take to ensure their safety while in a hazardous location.
- Always wear the correct PPE. Each class, zone, and division of hazardous location requires a different type of protection. Some may require full-body suits to protect the worker from ambient conditions and excessive heat. In other places, workers may only need gloves or a simple respiratory device.
- Establish and follow safety procedures. A large number of accidents in industrial environments occur due to carelessness and human error. Written instructions, signage, and periodic training ensure all workers know the rules and are motivated to follow them.
- Understand the risks of an environment before entering. Workers should understand the unique dangers of their work environment before they begin work. Information such as what tools are safe to use, how long they can risk exposure, and what challenges they may face (limited vision, compromised motion, etc.) within.
- Know what to do if an accident happens. In some cases, damage can be quickly contained with the right actions. Workers should understand things such as the location of emergency equipment, lock-down procedures, and who to contact when an event occurs.
These lessons are an important part of safeguarding the people and property that make industrial operations successful.
Benefits of Formal Training
How do employees benefit from formal training in OSHA safety regulations?
- Workers who are taught by a professional have a greater depth of knowledge than those who rely on simply reading the material. They retain more information, which makes them more effective in an emergency situation.
- Those who attend formal training are more likely to actually adhere to OSHA requirements. The training highlights the dangers of carelessness in a way that impresses the importance of PPE on industrial workers.
- Less accidents mean workers don’t experience serious threats to their long-term health and happiness. This decreases the amount of time they might miss due to accidents and allows them to continue supporting their families.
How do employers benefit from having formally trained employees on their payroll?
- Fewer accidents mean employers lose less productivity. Workers don’t miss shifts, which helps employers maintain deadlines and customer expectations.
- Non-compliance with OSHA regulations can result in large fines and penalties that threaten profitability. With the right training, companies are less likely to be punished for non-compliance.
- Protected workers feel more secure in their jobs, which means less turnover in the employer’s payroll. This also helps companies retain highly skilled, in-demand employees.
The Electrical Systems: Hazardous Locations seminar from NTT Training teaches industrial workers how to apply OSHA standards in their daily work. Instruction includes performing basic installations, identifying hazardous locations, and steps to take to protect against potential dangers.
Contact our representatives to schedule your training session.
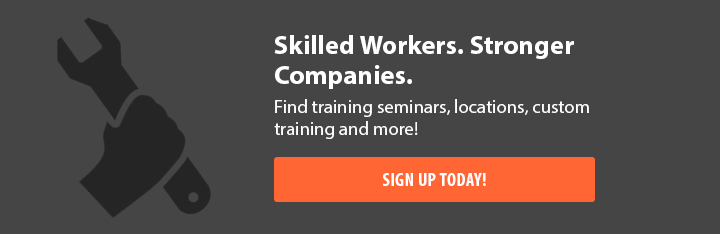